The Anatomical Pathology laboratory at the Cardiff and Vale University Health Board services the needs of a sizable local population, as well as specialist services further into Wales and other surrounding areas. Here Pathology in Practice learns how a commercial partnership has enabled significant improvements in reducing errors and lost samples by implementing new systems for sample tracking and storage.
While procedures exist in every anatomic pathology (AP) laboratory to protect samples in the diagnostic process, errors still can and do occur. There are three areas in the AP laboratory workflow where errors are known to occur frequently and where there are common inefficiencies: block archiving and retrieval,1 slide archiving and retrieval2 and pre-analytics, specifically pre-processing.3 Since 2016, Cardiff and Vale University Health Board (CVUHB) has been making consistent improvements and investments to address the need to ensure positive identification and tracking of samples in the AP laboratory. These changes have also had positive impacts upon productivity and helped to address case growth, despite the continuing shortage of qualified laboratory staff in the labour market and increasing budget pressure. There were additional challenges for CVUHB in the retention and storage requirements for blocks and slides.
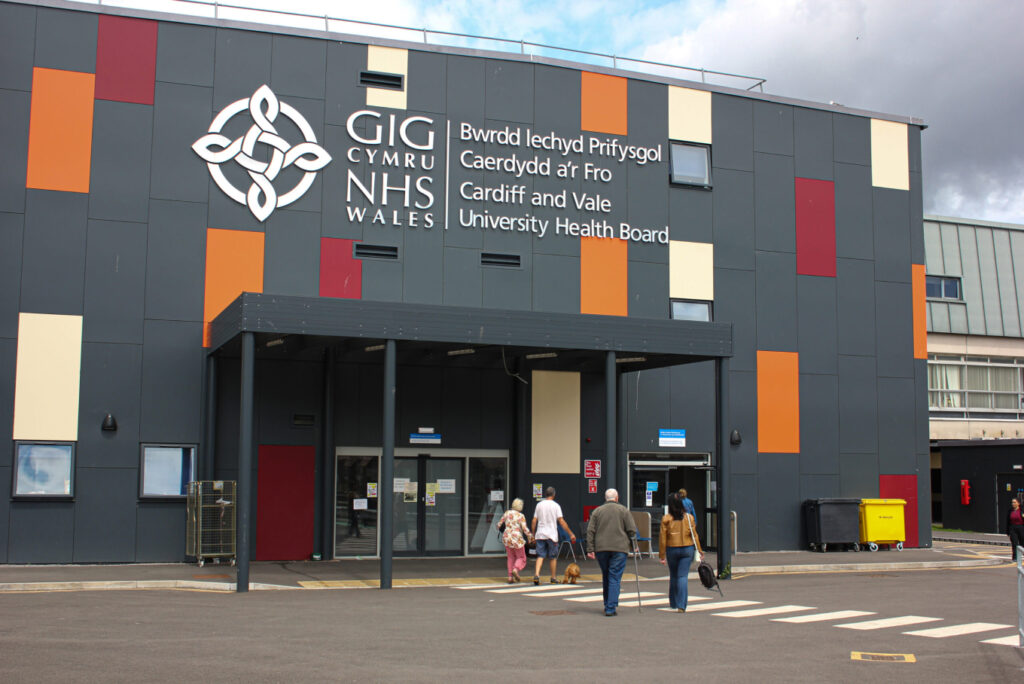
According to The Royal College of Pathologists (RCPath), a laboratory must store blocks and slides securely (in case of recall for further investigation or treatment) for a minimum of 30 years. In some cases this retention requirement can be even longer depending upon the complexity of the case or the age of the patient. Other countries and specific healthcare systems can have even longer retention periods, up to an indefinite period. This retention requirement presents another unique challenge for CVUHB and other AP laboratories that are experiencing greater caseloads based on growing disease incidence rates. These challenges were addressed over a series of years through an ongoing partnership with Dreampath Diagnostics and implementation of three Dreampath systems.
Laboratory details
Cardiff and Vale University Health Board is one of the largest NHS organisations in Europe and first opened in 1971. It employs approximately 14,500 staff, and spends around £1.4 billion annually on providing services to a population of over 472,000 people living in Cardiff and the Vale of Glamorgan. It also serves a wider population across South and Mid Wales for a range of specialties. CVUHB is a regional neurology and neurosurgery centre as well as regional centre for HER2 breast cancer screening. Lean workflow is a key part of CVUHB’s practice, enabling it to maximise throughput and achieve best possible turnaround times with minimal costs.
The AP laboratory at CVUHB is responsible for carrying out processing of patient tissue for diagnosis of cancers and other diseases. It is designed for 50 fulltime employees (FTEs); however, it has been operating at a FTE deficit based ona shortage of qualified laboratory staff. CVUHB manages around 90,000 specimens annually. From those 90,000 specimens, about 197,000 paraffin tissue blocks and 334,000 sections are produced. There has been a consistent 5% annual increase in the production of blocks.
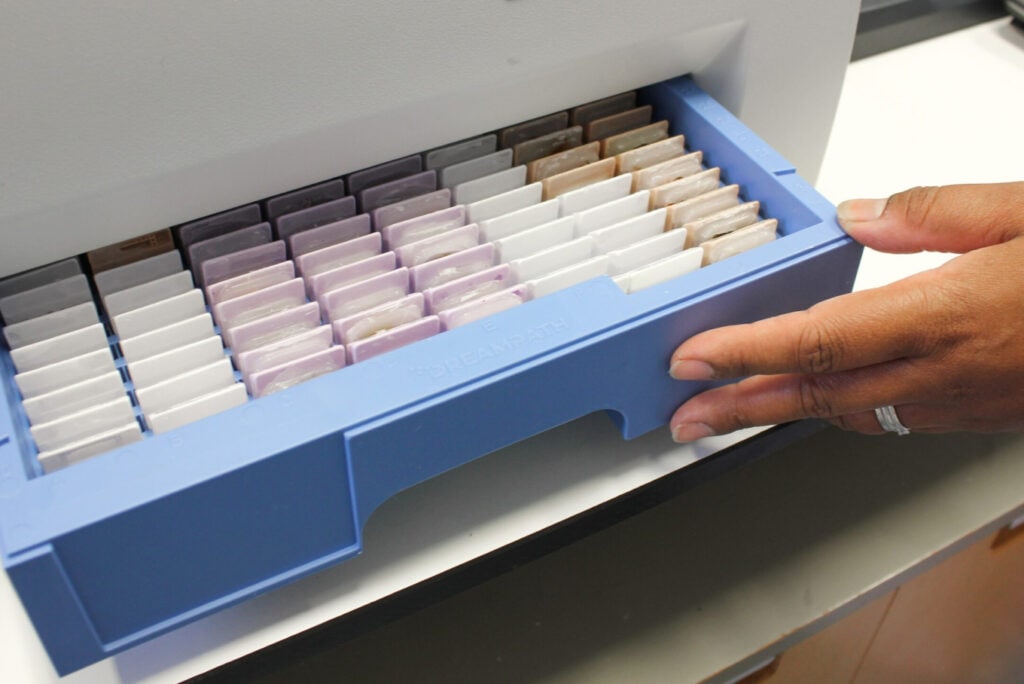
Tissue block archiving and retrieval
The Health Board placed its initial focus on the workflow for archiving and retrieval of tissue blocks. Previously, the laboratory used cardboard boxes to store patient blocks. An average of over 360 blocks per day meant that this was a very labour-intensive process with risks associated with misfiling a block. Such an error can have significant implications for patients. In addition, advances in immunohistochemistry and molecular testing mean increasing frequency for block retrieval. The manual re-archival process of ordering the blocks sequentially adds to the time and labour burden, and increases the potential for error.
All blocks are labelled with a unique identifier – an accession number – which is used to identify patient cases. Two dimensional (2D) barcodes on the blocks encrypt the accession number. Blocks are also scanned upon sectioning, and the unique barcode is also printed onto the corresponding slides for continued traceability throughout the workflow. Cardiff first partnered with Dreampath Diagnostics in 2016 with the Fina block management system (then known by the name Arcos). The goal was to improve efficiency within the department and reduce the risk associated with lost or misplaced patient blocks. The Fina system files tissue blocks in plastic trays and does not require sequential ordering. Each block is identifiable by a unique barcode. Each Fina tray holds up to 240 blocks and the system scans, photographs, and records each block in a database with a precise location.
Following completion of this step, the tray is placed into a purpose-designed cabinet for storage and archival. User- selectable locations can be created in the system to map the exact location of cabinets and trays. Several different locations (or zones) can be created – such as ‘laboratory’, ‘store room’ or ‘basement’ – making trays easily re-assignable to a zone. Trays and blocks are all barcoded for complete traceability, and all data are stored in the system, eliminating the requirement for manual sorting.
An important, yet often misunderstood, security aspect of the Fina system is that block locations are no longer obvious, unlike the traditional method of block storage where dates are marked on boxes and trays. This helps prevent the unauthorised removal of blocks from trays. Any block retrieval must be carried out by identifying the required block and retrieving it using a clearly defined process with the Personal Digital Assistant (PDA) that is part of the Fina system. This establishes a level of traceability and security for patient samples not previously seen in the laboratory. Upon proper retrieval of a block, the identity of the requestor as well as a reason for removing the block must be entered. Reason codes carry predefined timeframes for the anticipated return of the sample. For example, pulling a block for a reflex test may carry a 48-hour anticipated return time while sending a block to a different facility for a second opinion may carry a two- or three-week anticipated return time. These timeframes are part of an automatic ‘Samples out’ report that helps laboratory staff monitor samples out of the system and when they are due to be returned. The Fina system utilises data back-up in three distinct locations to ensure data are not lost due to a catastrophic event. Data are stored: i) within the scanner itself; ii) on the host computer; and iii) on the facility’s network drive.
Universally readable back-up systems mean that there would never be an issue of losing patient sample location data. With investment in the Fina system, considerable time and cost savings were immediately realised at CVUHB, and those savings have grown in the following years as caseloads have increased.
«As cancer incidence rates grow and the volume of samples grows, sample tracking is important to provide a necessary level of patient safety.»
Kita Williams, Dreampath Commercial Development Director
CVUHB staff have found that the system offers assurance of quality around the block filing process. While it is difficult to quantify the exact reduction in risk for lost or misplaced blocks and potential impact upon patients, it is clear that the Fina system delivers real benefits to safety and workflow. Scott Gable commented about Fina: “I like it a lot. It is a brilliant bit of kit! Location-based archiving is the way forward – Amazon have been doing it for years.”
Improving slide archiving and retrieval
Workflow around archiving and retrieval of microscope slides was improved in the same manner as the workflow for tissue blocks using a similar Dreampath system: Crystal. The Crystal system operates on the same premise as the Fina system, however, the samples are oriented in a different way. Historically, microscope slides were sorted in numerical order and stored in drawers in a manner where the label area containing the case numbers or unique identifier was not visible to the person retrieving a slide. This resulted in additional time and frustration with pulling archived slides.
The Crystal system uses a completely different approach for storing slides where the label area of the slides is always visible. This accelerates and simplifies slide identification and retrieval. Furthermore, the highly tedious and laborious task of placing slides in sequential order in a drawer is not required when using the Crystal system. This saves valuable technician time in the archiving and retrieval process.
Improving the pre-processing workflow with Hydra
After many years of using the Fina and Crystal systems, CVUHB staff were looking to make additional improvements to the AP laboratory workflow in order to reduce errors and lost samples at the tissue processing step. Consequently, the Dreampath Hydra system was introduced at CVUHB in October 2022 for a 12- week observational study to assess its impact on the pre-processing workflow and ability to reduce or eliminate errors associated with sample loss. The Hydra system was proposed as a solution to track the movement of samples with even greater accuracy and with traceability, and an added benefit of the Hydra system is its ability to ensure the accuracy of tissue processing schedules and fixation times.
As a part of this study, an updated workflow was also instituted to properly incorporate the Hydra system and recognise all of its benefits. The intent was to reduce manual tasks in the preprocessor workflow that are prone to human error, while enabling accurate and definitive monitoring of processing schedules, reagents used, times, and user activities to enhance the traceability of samples throughout the laboratory until final archiving.
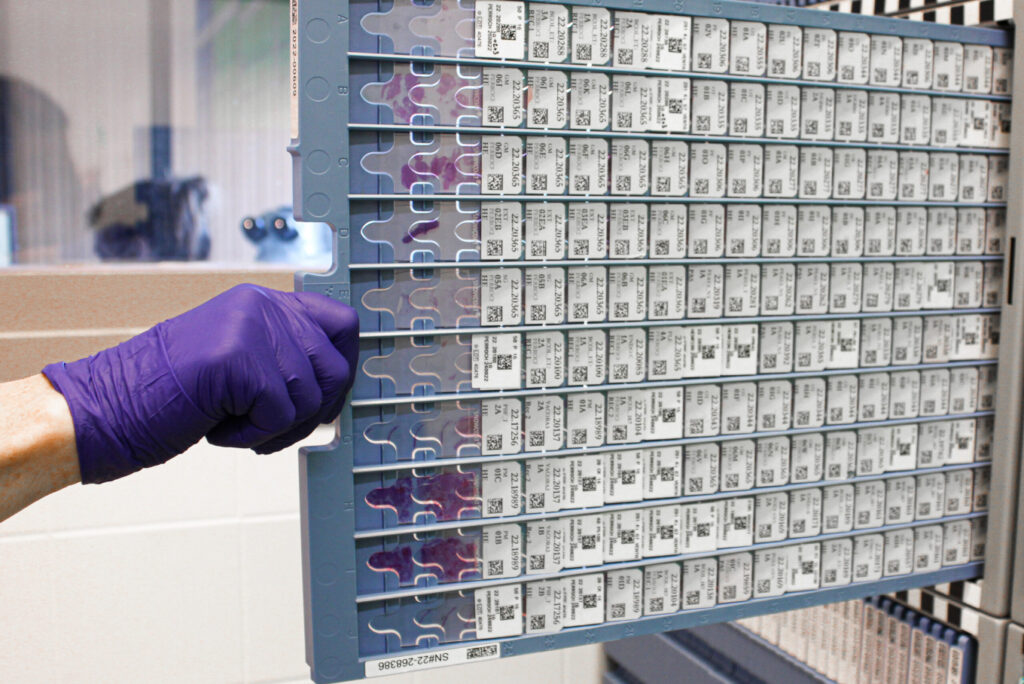
The installation of the Hydra system at CVUHB means that every tissue- processing basket and each individual tissue cassette is scanned prior to entering the tissue processor. Data are recorded by a verified user who is logged into the system. This establishes proper chain-of-custody for tissue samples. The user is able to allocate baskets to a processor that is automatically recognised by the Hydra software. The processor schedule, the data for each individual cassette, as well as the actual photographic image of the basket is stored in a folder connected to a network drive. The number of cassettes in the basket is automatically counted, as is the time that the scan occurred. The Hydra system can accommodate a delayed or immediate tissue processor start and the software indicates when the end time of that processing run will be. There is the option at the end of the processing run to rescan the baskets to provide reconciliation of what was put on the processor compared to what has come off, in the event any late cassettes were added to the processing basket after the initial scan.
Adding the Hydra system to the preprocessor workflow, CVUHB removed the step of taking a digital picture, transferring the image file, analysing the image, and recording run data. All of these were manual steps. In the event of any issues that required investigation, confirmation, and correction, the quality manager had to refer to the digital image, count the samples in the image, and identify the sample in question. This was a completely manual process that was especially time-consuming and inefficient, with potential for errors.
Introducing the Hydra system and a new workflow at CVUHB from October 2022 to January 2023 resulted in a reduction in time associated with reconciling lost or misplaced samples in the laboratory workflow.
- This reduction went from as long as three days to as short as a couple of hours (nearly an 82% reduction)
- All misplaced samples were properly recognised and corrected within 2.5 hours as a consequence of the new Hydra system workflow and tracking database
- 96 potential manual touchpoints were eliminated in the preprocessing workflow
- Time associated with scanning cassettes and baskets was reduced by 91%. These improvements created a more efficient laboratory workflow, reduced the stress of AP laboratory staff, and improved turnaround times.
82%
time saving in reconciling lost or misplaced samples
91%
time saving in scanning cassettes and baskets
96
manual touchpoints eliminated in the preprocessing workflow
The Hydra system and software also allowed for identifying potential issues related to sample quality stemming from the tissue processor. By tracking these issues back to an individual processor and schedule, other potential samples affected may be identified before issues occurred. This reduces the laboratory’s cost of poor quality (COPQ) and also reduces the risk associated with compromised tissue and the need for potential re-biopsy. This was an especially large benefit for the laboratory staff given the tedious and time-consuming nature of checking every reagent in a tissue processor.
The Hydra system and software also allowed for identifying potential issues related to sample quality stemming from the tissue processor. By tracking these issues back to an individual processor and schedule, other potential samples affected may be identified before issues occurred. This reduces the laboratory’s cost of poor quality (COPQ) and also reduces the risk associated with compromised tissue and the need for potential re-biopsy. This was an especially large benefit for the laboratory staff given the tedious and time-consuming nature of checking every reagent in a tissue processor.
ANATOMICAL PATHOLOGY
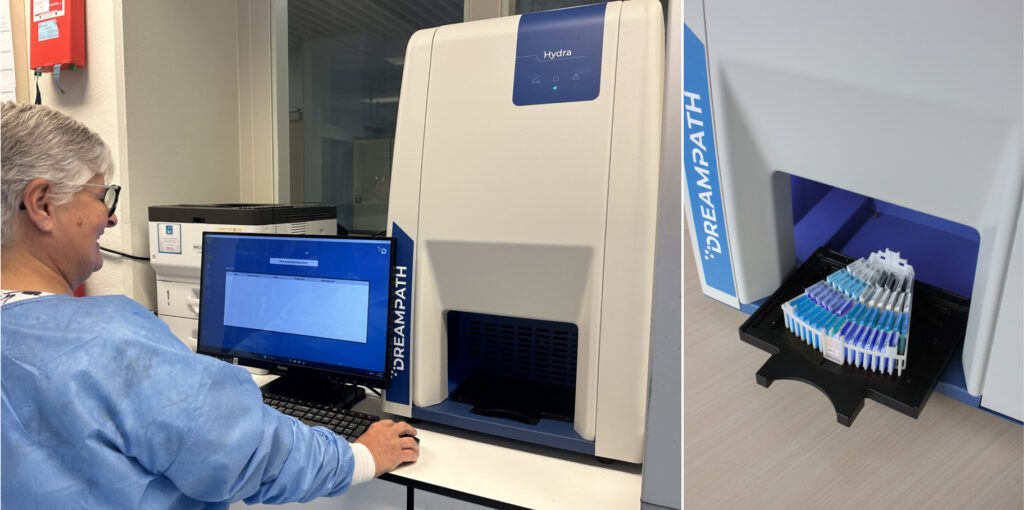
Impact on laboratory staff
Introduction of these three systems and associated workflow changes also provided several additional benefits to the laboratory staff through increased job satisfaction, decreased stress around potential sample loss, and reduced exposure to chemical fumes. Introduction of the Hydra system eliminated mundane manual tasks and enabled the CVUHB staff to stay focused on the critical aspects of histopathology to facilitate a fast and accurate diagnosis. With fewer qualified laboratory personnel available to do an increasing volume of work, it is important to reduce tedious and laborious efforts that add little value to the diagnostic process. Further, Hydra’s incorporation of ventilation and filtration decreased laboratory staff exposure to fixative fumes.
Looking ahead
While already experiencing improved workflow with Fina and Crystal for many years, the Hydra system and the new and improved workflow that accompanies it will further simplify and improve laboratory processes at CVUHB. And future software enhancements will continue to improve processes and sample tracking and reconciliation. In the next version of Dreampath software, scan data from the Hydra system will be shared with the Fina system and provide expectations on likely archiving time. This makes it easy to assess turnaround times and also identify delays in the workflow before chasing a result. It also simplifies sample reconciliation before archiving tissue blocks.
Interfacing with the laboratory information system (LIS) was not a part of the observational study with Hydra at CVUHB, but it will be part of final implementation. This LIS interface enables an even more accurate tracking of a sample’s progress through the laboratory, giving clinicians data-driven expectations of when a diagnosis will be available.
Taken together, the three Dreampath systems (Fina, Crystal and Hydra) provide specific solutions to problems that have long plagued the AP laboratory. This is evidenced by the measurable improvements experienced at CVUHB and their continued partnership with Dreampath Diagnostics. “We’ve enjoyed working with Dreampath on this effort. They have been receptive to our feedback and have been easy to work with. They really understand the AP laboratory and how it works,” said Gable. “We’re looking forward to partnering with them on more projects in the future.”
References
- Costes Martineau V, Dumas L, Leventoux N. A Cure-All For Block Management Woes? The Pathologist 2016 (https://thepathologist.com/inside-the-lab/a-cure-all-for-block-management-woes).
- Giannini C, Oelkers MM, Edwards WD et al. Maintaining clinical tissue archives and supporting human research: challenges and solutions. Arch Pathol Lab Med. 2011;135(3):347-353. doi:10.5858/2010-0044-SA.1
- The Royal College of Pathologists. The retention and storage of pathological records and specimens (5th edition). RC Path / IBMS 2015 (https://www.rcpath.org/resourceLibrary/the-retention-and-storage-of-pathological-records-and-specimens–5th-edition-.html)