Challenge
Address the last missing piece for sample tracking in the AP workflow at Pathologists Bio-Medical (PBM) PathGroup: sample pre-processing
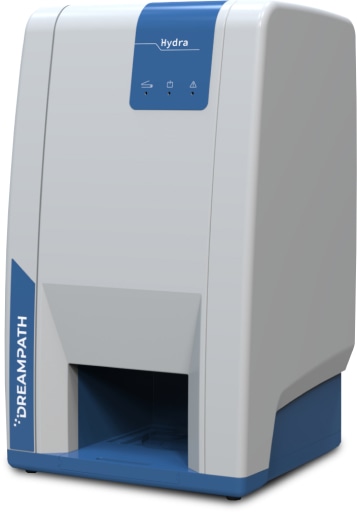
Background
- Large, regional laboratory with over 50 years of experience in providing diagnostic services in Texas and surrounding areas.
- Long history with one of the largest health systems in North Texas; a part of PathGroup since 2019.
- 600 to 1000 blocks per day; 1500 to 1750 slides per day
- Had been working to create a solution for tracking samples in the AP lab through the use of barcodes, scanners, and high resolution cameras to track samples throughout the lab and closely monitor steps. This was a very time consuming and costly effort pursued over the course of several years. Despite all the time and effort, the preprocessing step in the AP workflow was still a gap in sample traceability.
Approach/Goals
Three primary goals in implementation of the new workflow and system.
- Support future growth – Sample tracking is important to determine how to better apply lean principles. Further, labor shortages impacting the AP segment mean staff must be better utilized.
- Improve quality – Ensuring sample quality is increasingly important in AP, and researching quality issues in preanalytics is time consuming. Data and traceability of samples at preprocessing was needed to reduce the potential for compromised, lost, or misplaced samples.
- Advance lab safety – Data about samples at preprocessing could reduce the potential for compromised, lost, or misplaced samples. However this needed to be complementary to the existing workflow.
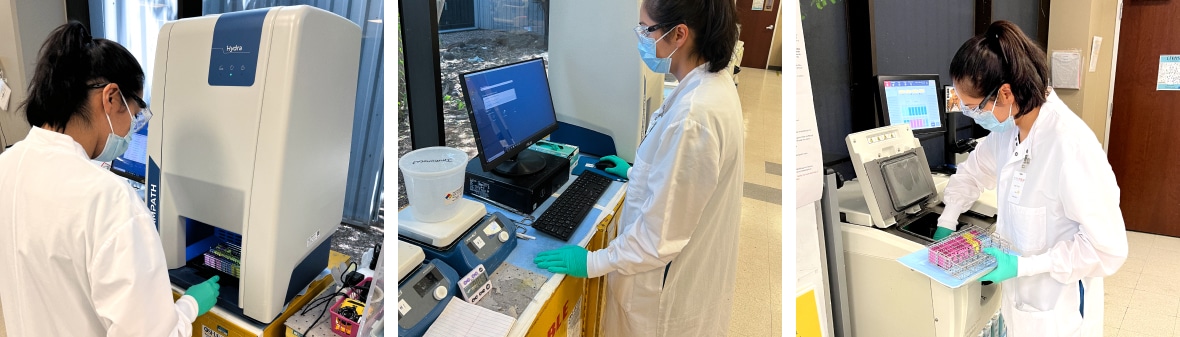
Results
- The Hydra optimization phase lasted for about seven weeks. While the initial scanning of cassettes took longer than the prior method using a digital camera, the benefit of Hydra was that cassette data was immediately available for use rather than requiring manual interpretation of the digital image.
- Shortly after full implementation of Hydra into their workflow, the lab staff experienced three events where the Hydra system data and new workflow demonstrated value.
- Missing cassette at preprocessing: A missing cassette on a large case was reported. In searching the archived lab video footage of when the cassette should have been processed, the lab staff was still unable to locate the missing cassette. However, when the Hydra power user accessed the Hydra system data, she realized that the cassette had never been through the Hydra system. This immediately narrowed the search area for the missing cassette to preprocessing. As a result, the missing cassette was quickly recovered and expedited through the diagnostic process.
- Missing cassette at post-processing: A block that was scanned on Hydra was never scanned at embedding and was subsequently identified as missing. This immediately narrowed the search area for the missing cassette to post processing. The investigation revealed that when a technician was unloading a basket from a tissue processor, they dropped the basket and the missing cassette was dropped on the floor. (It was actuallyfound under the tissue processor.)
- Impact of improper processing: When a tissue sample did not survive processing, Hydra data was accessed in order to troubleshoot. The processor used to process the sample was easily identified with Hydra data. Lab staff measured the alcohol concentrations on the processor with a hydrometer, which revealed that one of the alcohols was outside of the concentration on the screen display. Hydra data also revealed that the sample was assigned a longer than necessary protocol, contributing to the loss.
- Each of these investigations took the lab staff 15 – 20 minutes, whereas they would have been 3-4 hour efforts without the Hydra system and data. These investigations led to valuable insights in how to improve lab processes further.
Conclusion
- The Hydra system and corresponding workflow has met its goal to enhance safety and quality in the AP workflow. It has also improved the overall efficiency of the lab staff by simplifying tasks, reducing/eliminating touchpoints, and delivering greater levels of lean workflow. By narrowing the search area for a missing sample to pre or post processing, hours of already scarce lab staff time can remain focused on patient care.
- Further, the data generated by the Hydra system, allows for a greater degree of accuracy for projecting equipment needs and growth planning.